801-755-4296
CLIFF HARDLE

LITTLE GIANT LADDERS
Improving production efficiency
Little Giant Ladders produces industry leading aluminum and fiberglass ladders in Springville, Utah. This was a class project for my MBA Quality Improvement class.
Scope: Address starvation of rungs at the riveting station in assembly line.
Riveting station for new fiberglass ladder product line is frequently starved for welded aluminum rungs. Further, there was a 30% defect rate in welded aluminum rungs.

WHAT'S THE HOLDUP WITH PRODUCTION?
Little Giant had recently began production of a new model of ladder. However, production was not going as smoothly as planned and was encountering a variety of quality control issues and delays. Our task was to find out what was holding up production and provide recommendations to fix the problems.
GAINING UNDERSTANDING

OBSERVATION AND INTERVIEWS
To gain a better understanding of the problem we began speaking with the people closest to the problem. Technicians, managers, and assembly workers. We also observed them as they worked because often what people say and what they do are different things.

UNDERSTANDING THE PROCESS
We broadened our view by learning about upstream and downstream processes in the assembly line. We discovered possible problems occurring in production of parts before reaching the riveting station and even identified areas where products suffered damage after assembly, such as being stored on concrete flloring where ladders were susceptible to scratching.

UNDERSTANDING QUALITY CONTROL
We also wanted to know how Little Giant was currently managing quality control. We found a lot of interesting methods and touchpoints throughout the system. We also found that some could be consolidated and steps added in different parts of the process.

CREATING A PROCESS MAP
After becoming acquainted with Little Giant's production line we created a process map. This helped us to get a clear overview of the process, where quality control was happening, where bottlenecks were occurring and where errors could appear.
DEFINING THE PROBLEM

TRACKING DEFECTS
From our initial research we found out that welding defects in aluminum ladder rungs were a huge issue causing delayed production. Not only were issues happening but there was not a clearly defined process for tracking and dealing with defects. Defective pieces were piled up next to welders and delays were not being communicated upstream.
LEARNING WELDING THE PROCESS
We spent time with the technicians who oversaw the welding process to gain some more insight. We learned that specific types of defects were dependant on different techniques used by technicians in inserting the pieces into the automated welders. Further, welding defects were not being communicated to managers who could program corrections into the robotic welders. There was a lot of room for error.


STATISTICAL PROCESS CONTROL
We new we needed to start tracking defects to make some solid recommendations. This is were we began using statistical process control. We found out that nearly 30% of welded rungs were defective, we even started to learn which areas of the parts were most susceptible to errors.
METHOD FOR TRACKING DEFECTS
We also developed a method for tracking defects in the welded rungs. This method was easy to understand and implement.


LARGE BINS SLOWING PRODUCTION
We also discovered that the bins of finished rungs were too large. Production workers would wait for bins to fill before handing them off to the riveting station. This was leading to unnecessary delays at the riveting station.
DEVELOPING A SOLUTION

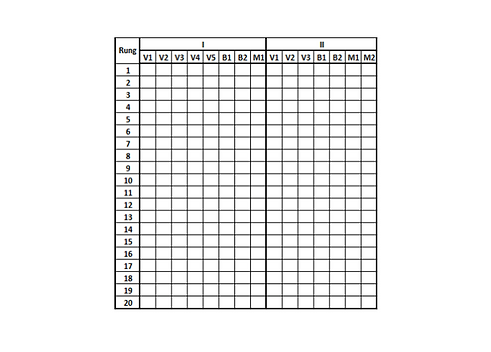
CAUSE AND EFFECT DIAGRAM
We used a cause and effect diagram to help us get down to the core of the problem.
We found:
●The slim side of the baseplate is too narrow
●Frequency of preventative maintenance on welder allows for defective welds
●Large rung carts allow production line workers to assemble batches that are inefficiently large
IMPROVED TRACKING AND REPORTING
We also developed a system for tracking and reporting based on our defect identification tool. This would allow that managers were aware of specific problems, instead of chasing unkowns, and were better prepared to solve them.
RECOMMENDATIONS
REDESIGN PLATE BLANKS AND BLANKING TOOLS
Increase thin side edge margin
Tighten tolerances of punched slug hole with rung size
Change weld start/stop location from thin side
Large upfront cost, minimal ongoing costs
IMPLEMENT STANDARDAIZED QUALITY INSPECTION AND DOCUMENTATION METHODS
Easy to identify problems quickly
Risk: cost of production worker's time to document data
PERFORM TPM ON ROBOTIC WELDING MACHINES
Perform TPM (total productive maintenance) every 50-60 rungs
REDUCE RUNG BIN SIZE TO REDUCE WIP
Current bin size starves riveting station unnecessarily
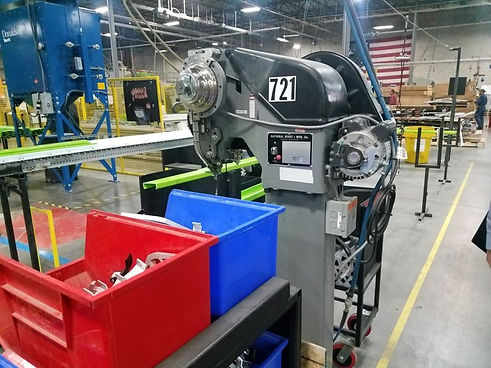